December 2023 Issue Table of Contents
The raw materials industry produces billions of tonnes of mine waste per year. Given increasing metal demand and the global appetite for waste reduction, strategic opportunities to minimise its production must be embedded across the life-of-mine. Adopting a geometallurgical approach to total deposit characterisation—where mineralogical and geochemical data are routinely collected and used to model geoenvironmental domains—offers profound benefits for improving the understanding of the composition and environmental impact of different residues. Using established and emerging technologies, from handheld instruments and core scanners to synchrotrons, throughout a mine’s life—starting already during exploration—may assist the raw materials industry to reduce their waste footprint and adopt circular economy principles.
1811-5209/23/0019-0371$2.50 DOI: 10.2138/gselements.19.6.371
Keywords: Mine waste; tailings; circular economy; critical metals; short-wave infrared
INTRODUCTION
Our global community hit a milestone in 2023: 8 billion humans. By 2050, this will have grown to 9.7 billion. With this comes increasing pressure on our natural resources to sustain the wellbeing of the growing population. It is the global raw materials industry that faces the challenge of finding and developing the ore deposits needed to sustain this demand. However, once found and mined, an even bigger challenge is posed. How do we manage the resulting mine waste? Approximately 100 Gt of mine waste is produced annually (Tayebi-Khorami et al. 2019). Taking just one commodity, copper (a key metal in all electrical infrastructure), Valenta et al. (2023) predicted tailings production to increase from 4.3 Gt/y in 2020 to 16 Gt/y in 2050. In total, 858 Gt of mine waste could be produced for this metal alone up to 2050. Typically, mine waste is placed into purpose-built repositories or landforms where it remains indefinitely unless another use for it is found (e.g., tailings used as backfill material for mining-related cavities in underground mines).
Since the publication of the Elements article, “Mine Wastes: Past, Present, Future” (Hudson-Edwards et al. 2011), the attitude of industry towards mine waste has evolved. This has been triggered by two factors: 1) the rise of critical raw materials (CRM) needs driven by our attempt to combat climate change; and 2) the growing importance of environmental, social, and governance (ESG) standards. This article explores opportunities for integrating geometallurgy (Frenzel et al. 2023 this issue) across the life-of-mine to reduce environmental risks associated with mine waste materials. It also considers how the global mine waste footprint, calculated to be approximately 50,790 km2 (Maus et al. 2022; almost the equivalent area of Costa Rica or Bosnia and Herzegovina), could be reduced.
WHAT ARE MINE WASTES?
Mine waste, as a general term, is summarised by Hudson-Edwards et al. (2011) as uneconomic, solid, and liquid materials found at (or near) mine sites. They are heterogeneous materials including relatively coarse-grained waste rock and slags, fine-grained tailings, ashes and flue dusts, and chemical- and metal-bearing waste water. Waste materials are produced at all stages of the industrial value chain of raw materials, with mine waste subdivided into three types: waste rock, tailings, and metallurgical residues (Fig. 1). During mine development and mining, non-ore rocks are removed, generating large tonnages of very coarse, highly heterogeneous material collectively termed waste rock. Both open cut and underground mining activities will produce these materials, albeit with the first producing much higher volumes. Waste rock is just a geological material and can consist of igneous, metamorphic, or sedimentary rocks that may be affected by hydrothermal alteration or surface weathering. The mineralogy, chemistry, and texture of these materials can be heterogeneous, with their physical properties varying in response to this compositional complexity. For example, particles can range from clay size (with a large available surface area for oxidation processes) to boulder size fragments (comparatively less reactive; Lottermoser 2010; Fig. 2A). Waste rock is typically trucked to the final waste landform (i.e., dump or pile), where it is carefully placed based on engineering design criteria informed by geochemical and geotechnical assessments.

Mineral processing follows on mining (Fig. 1), with a large variety of technologies applied to produce a mineral concentrate suitable for direct use or extractive metallurgical treatment (see Pereira et al. 2023 this issue). Independent of the chosen method is the production of a waste stream referred to as tailings (Figs. 1 and 2B). For context, 90%–98% of copper ore processed ends up as tailings (Valenta et al. 2023). Tailings consist of finegrained rock particles (10–300 µm) mixed with process waters. Tailings typically comprise residual ore minerals, gangue minerals, and secondary minerals that may form after deposition of the tailings (Lottermoser 2010). They are usually disposed via pipelines affixed with a spigot, into purpose-built dams or storage facilities for which several designs exist (Lottermoser 2010). Deposition of coarser and denser particles occurs proximal to the spigot point, with less-dense, finer-grained materials depositing distally. Tailings deposition can be seen as roughly analogous to sedimentary delta formation.
Metallurgical processing is undertaken to produce metals from mineral concentrates (Fig. 1; see Chetty et al. 2023 this issue). This process generates significant volumes of metallurgical residues, including slag, spent heap leach, residues, red muds, dusts, and waste waters. These can be very reactive and highly concentrated in environmentally problematic constituents. Slags, whilst variable in composition and texture (e.g., the relation between crystallised and glassy materials that comprise the slag) broadly fall into two main types: ferrous and non-ferrous. Mineral-like phases from the olivine, pyroxene, and spinel groups dominate, in addition to amorphous glasses of variable composition (Fig. 2C). Where reactive sulphides are present (e.g., pyrite), there is a high probability that acid and metalliferous drainage (AMD) will form under surficial conditions, as shown in Figure 2D.
After mine closure, mining, mineral processing, and metallurgical residue deposits, as well as mining voids (open pits and underground workings) remain on site and are the focus of rehabilitation efforts. Other types of waste generated at mine sites (e.g., municipal and plastic waste) are less significant in terms of tonnage and volume, and in the case of disused equipment, may even be perceived as an asset and sold.
PROBLEMS AND OPPORTUNTIES
If inadequately managed, mine waste can pose a range of physical risks (i.e., tailings storage facility (TSF) failures) and risks of (physico)-chemical pollution (i.e., AMD, noxious dust) to the receiving environment. Over the past decade, several TSF failures have featured very prominently to global society through modern communication channels including Mt Polley (2014, Canada), Samarco (2015, Brazil), Brumadinho (2019, Brazil), and recently Jagersfontein (2022, South Africa). These can mostly be attributed to design deviations and monitoring gaps and have catastrophic consequences. Whilst the causes of these failures have varied, it has been acknowledged that the post-depositional mineralogical (described in Moncur et al. 2015) and also textural evolution of tailings is not always accounted for in the design phases, as acknowledged by Robertson et al. (2019). This highlights the importance of understanding all particle properties of deposited tailings, as well as changes that may occur after deposition. However, such detailed information is rarely captured. Instead, only bulk properties like slurry density, percentage of solids, particle size distribution, and limited chemical data (e.g., Cu, Fe, and S in a copper operation) are routinely recorded. There is a clear opportunity to gain more detailed knowledge about the compositional and textural characteristics through geometallurgical studies. This knowledge may improve the understanding of the physical behaviour of the tailings material and may form part of an integrated dataset required to avoid catastrophic physical failure, ideally before deposition and, if already in place, to enhance the possibility of monitoring the wellcharacterised material.
In pollution terms, Lottermoser (2010) explained that mine waste is considered problematic if it contains or may generate hazardous substances (e.g., heavy metals, metalloids, radioactive elements, process chemicals, acid-generating minerals, and/or asbestiform minerals). Iron sulphide minerals (e.g., pyrrhotite, pyrite, arsenopyrite, marcasite) are commonly associated with metalliferous ore deposits, and can be found in mining, mineral processing, and/or metallurgical wastes. If they undergo oxidation, sulphuric acid will be generated and low-pH waters will form, resulting in AMD (Hudson-Edwards et al. 2011; Fig. 2D). In acidic surface and ground waters, the mobility of metals and/or metalloids (e.g., Al, As, Fe, Zn, Pb, Cu, Ni, Co) is greatly promoted with associated high sulphate concentrations. The mobilised metals then enter the receiving environment where they may cause severe environmental impacts to flora and fauna.
The United Nations declared AMD the second biggest global environmental challenge after climate change (Kefini et al. 2017), as typically, once AMD has started to form, it is very difficult to contain (Lottermoser 2010). Whilst the engineering design of mine waste facilities attempts to prevent AMD, the majority fail to do so in the long run. AMD treatment methods are then required, with two types, active or passive treatment, typically being implemented. Active methods include the application of alkaline chemicals to precipitate metals, and other techniques such as adsorption. Passive treatment of AMD may involve biological treatment with constructed wetlands, and/or chemical treatment with limestone drains and sulphate-reducing bioreactors (Kefini et al. 2017). Whilst offering some environmental benefits, these treatment options are largely regarded as expensive and may not be sustainable long-term (i.e., they may be technologically complex, requiring regular maintenance; Ighalo et al. 2022). To reduce the risk of AMD, sulphide-bearing tailings are often overlain by engineered or vegetated covers. These covers are often not sufficient to de-risk a site. Penrose et al. (2022), for example, presented a case study where wombats had burrowed into a vegetation cover placed over arsenic-rich mine tailings in Tasmania and were exposed to heavy metals. There is a clear opportunity to use data acquired through thorough mineralogical characterisation of ores and major waste types already during exploration/pre-feasibility stages to identify not only all viable commodities, but to also quantify environmental risks arising from resulting residues.
Not all mine wastes pose an AMD threat, as they do not all contain reactive sulphides. However, if ‘inert’ wastes are sub-aerially deposited, e.g., waste rock and slag piles (Fig. 2), then noxious dusts can be generated through weathering processes. The Broken Hill lead–zinc–silver mine in Australia serves as an example. Mining commenced at Broken Hill in 1885 and is still ongoing. During its life-of-mine, lead-rich dust has been generated from both mineral processing operations and mine wastes, including a historic slag pile. Metal-rich dusts have been deposited into adjacent gardens and parks, and lead can enter the blood stream through hand-to-mouth soil contact (Dong and Taylor 2017). This causes very significant health risks. A thorough mitigation program is thus currently in place, including a reduction of waste pollution sources to soils and waters and development of a waste management plan for the entire mine site (New South Wales Environment Protection Authority 2016). Another excellent example of noxious dust generation by mining wastes are the crocidolite-bearing tailings around Wittenoom in Western Australia. The asbestiform crocidolite fibres in the tailings pose human health risks (mesothelioma; Rogers 2018). Dust suppression methods, such as the introduction of engineered or vegetation covers, are used to limit the impact of noxious dusts.
Common to all the mine waste problems described above is the need for better characterisation of the mine-waste properties (chemistry, mineralogy, texture, geotechnical parameters, including porosity and grain size, and even hardness) during emplacement and beyond. With increased importance placed on environmental sustainability, the mining industry finds itself at a crossroads. It can either maintain current waste management practices, which will become increasingly challenging as higher tonnages are generated to meet future ‘green’ needs (relating to the energy transition, and need for CRM mentioned in the introduction). Or it can challenge the entire paradigm of mine waste management by adopting an action (i.e., introducing preventative measures, limiting the occurrence of environmental problems early in the life-of-mine) rather than a reaction (i.e., managing issues once they have occurred) approach. Using medicine as an analogue: preventing rather than curing disease.
SOLUTIONS
In the previous section, several opportunities were highlighted to minimise residue volumes and to predict, as well as limit, the environmental impact that mine waste will have in the future. In addition, economical aspects will change over time with increased demand for certain elements and materials present in wastes, offering an economic opportunity that will be of interest in decades to come. Turning wastes into resources must be the final goal to avoid all the risks and mitigation measures discussed above. However, this will only be possible if we know what these wastes are (geometallurgically speaking) in advance (in situ) or once deposited (ex situ). Considering this, the technological innovations for multi-scale ore characterisation (in both 2D and 3D) and the data sets collected, as described in Butcher et al. (2023 this issue), must also be applied to mine waste characterisation. If this information is routinely and continuously collected over time, then better geoenvironmental (and economic) decisions can be made across the life-of-mine. The following section outlines key considerations and examples of how this can be implemented.
Exploration Phase
At early stages (i.e., exploration, pre-feasibility), areas (or domains) associated with increased environmental risks (e.g., higher pyrite content or arsenic concentrations) in and around an ore body that is being explored should be delineated. Such an assessment should include geotechnical stability as well as AMD risk. For the latter purpose, static and kinetic geochemical tests are the current industry-standard methods. Such tests were developed in the 1970s for the coal mining sector specifically to evaluate absolute acid formation and neutralisation potential. They have, however, been repeatedly criticised in the literature as an oversimplification for the more complex composition of metalliferous ores (Parbhakar-Fox and Lottermoser 2015 and references therein).
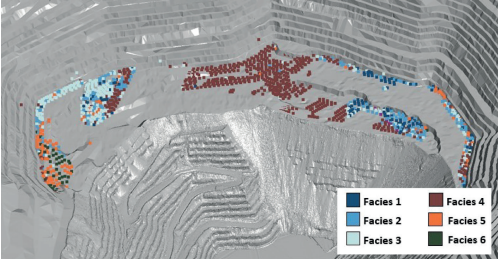
Whilst geostatistical approaches are now being taken to map spatial heterogeneity of geochemically important parameters in waste-rock piles, new technologies can also be used to enhance, or improve, the accuracy of these models. For example, technologies used in geometallurgical investigations can also be used for geoenvironmental domaining. These technologies broadly fall into two sub-sets: 1) hand-held instruments allowing for point measurements, including portable XRF (measuring elements from Mg to U), laser-induced breakdown spectroscopy (LIBS, having the added advantage of analysing lighter elements, such as the critical metal Li), hyperspectral imaging sensors (UV-VIS-NIR-SWIR), and mineral hardness testers including the EQUOtip and Hardness Impact Tester; and 2) instruments able to image larger areas, especially exploration drill cores, such as hyperspectral and chemical core scanning instruments, even including X-ray tomography. An example of their potential integration into routine geoenvironmental domaining workflows is shown in Figure 3.
Of these methods, hyperspectral technologies, also known as infrared spectral imaging drill-core techniques, are the most promising as they provide microstructural and mineralogical insights at the right scales to complement the geoenvironmental risk evaluation of a mineral deposit. Several recent developments have produced tailored workflows for evaluating geoenvironmental risks from hyperspectral imaging (Parbhakar-Fox 2019). Whilst there are associated limitations, e.g., many minerals are not spectrally active and the method only provides information from the sample surface at rather low spatial resolution (Laukamp et al. 2021; Butcher et al. 2023 this issue), this technology has the major advantage of rapidly collecting a high volume of mineralogical data about both the gangue and ore minerals in a core. Hyperspectral data are particularly suited to quantify the abundance of those minerals necessary to forecast AMD neutralisation potential and dust generation across a mineral deposit. The methods can also be used to identify other materials that are environmentally relevant such as clays for capping, aggregate materials, and ‘ore sands’ involving the recovery of quartz-rich sand during mineral processing (Golev et al. 2022).
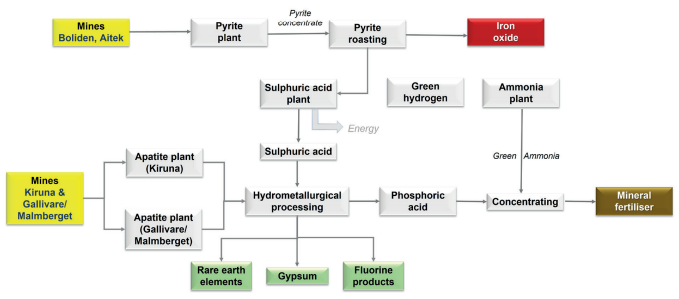
Production Phase
During the operational phases of mining, the transportation and deposition of waste is one of the most important factors to keep an operation on track to meet its production targets. One of the main sources of environmental problems, as mentioned in the introduction, is the large volume of actively produced waste materials. Fingerprinting of the mineralogy and chemistry of the waste is not common practice for most mine sites, as it can be impractical using current technologies, with very few examples of geospatial models available in the literature (e.g., Wilson et al. 2021). The development of 3D models for mining waste repositories will require the deployment of characterisation tools that can collect compositional data as materials are being deposited. Such sensors should be widely embedded across an active mine, as resultant data may also be useful to determine if there are potential repurposing opportunities. For example, hyperspectral scanning technologies may be used to obtain knowledge of the mineralogy of a bench face, albeit at very coarse resolution (e.g., Barton et al. 2021). These will give a first-pass insight into the mineralogical signature of a targeted area, and if compared against the geoenvironmental model, could be used as a way of very crude ‘waste control’.
Sensor-based technologies can be used to track the properties of waste. A wide range of sensors are both available and in development and show promise for sorting waste material (Robben and Wotruba 2019). Several of these sensors can help identify acid generating and non-acid generating materials, as well as several other elements of environmental interest that may need tracking during mining. Embedding such sensors as in-line monitoring tools will increase the knowledge of waste material properties and improve geoenvironmental management. An example includes blasthole scanning with hyperspectral scanners, like those scanning core, to inform not only the mine planning for ore optimisation but also help track the waste rock to the storage facility (Fig. 4).
The best practice would, of course, be the direct re-use of a residue stream for another industrial purpose, conforming to circular economy principles. One particularly obvious route is the use of mine waste as an alternative source of aggregates for civil engineering. A successful example of such re-use is the Vale factory in Brazil that transforms mining waste into products for civil construction, including interlocking floors, structural concrete blocks, or sealing blocks, among others (Vale 2020). The recovery of by-products, such as critical metals, is another possible route that is especially attractive for tailings, slags, or ashes. A highly innovative example comes from northern Sweden. Here, a pyrite-rich tailings stream of the Aitik copper mine is proposed to be used to generate sulphuric acid. This acid will then be used to extract a variety of products (phosphate, rare earth elements, gypsum, and fluorine products) from apatite that occurs in the tailings of adjacent iron ore mines (Fig. 5). Realizing such opportunities will create additional commercial value, which can then be invested in continuing to reduce mine waste volumes and therefore environmental risks.
Decommissioning and Closure
Although acting before the mine wastes are being deposited is by far the best solution, the overall economics are not yet routinely considering such options due to the lack of characterisation of mine wastes, such that re-purposing or re-processing options are never contrived or realised. The previous failure to understand mine wastes has resulted in existing mine wastes now being increasingly recognised as potential resources of metals and other sought-after materials, with circular economy principles also helping to drive this change in value perception (Kinnunen et al. 2022). Assessing the value of existing mine waste that has not been characterised during its deposition necessitates not only drilling and chemical assaying, but also full integration of quantitative mineralogical and textural assessments (Buettner et al. 2018). Appropriate strategies for invasive sampling and geostatistical modelling of the often-heterogeneous bodies of waste need to be continually developed and applied (e.g., Blannin et al. 2022). However, prior to invasive sampling, geophysical techniques could be routinely used, including microseismic, induced polarisation, and electromagnetic methods. These can improve the subsurface knowledge of a mine waste facility and help guide invasive sampling and volumetric calculations. Studies that have applied geophysical tools for characterisation and successfully integrated this mineralogical information include Moellehuara-Canales et al. (2021). Finally, processing technologies suitable for mineral and metal recovery from finest, low-grade, refractory, and partially weathered mine wastes need to be developed (Whitworth et al. 2022).
To address these challenges, a geometallurgical approach (collecting data to develop block models of metal deportment and geoenvironmental characteristics) to mine waste characterisation can be applied after mine closure with national programs focussed on this having already taken place in Europe (e.g., the Horizon 2020 funded SULTAN and NEMO projects). Similar research programs are also underway elsewhere, such as in the U.S. (Payne Institute for Public Policy, Colorado School of Mines) and in Australia (Geoscience Australia and several state governments collaborating with universities to build a national mine waste atlas). The raw materials industry, too, is investing in more research and development, including the Broken Hill Proprietary (BHP) global tailings challenge launched in 2020 and the zero-waste challenge of Oz Minerals. Real examples of businesses recovering value from tailings exist (e.g., re-mining of Au-bearing tailings of the Witwatersrand Au–U deposits, South Africa where part of the realised value is, in fact, the recovery of land near Johannesburg) or are emerging, including the Century Zn Mine and the Hellyer Pb–Zn–Au–Ag Mine. Both of these are in Australia where there is growing appetite amongst smaller exploration and mining companies to tap into this business opportunity.
OUTLOOK
One of the ultimate goals for the global raw materials industry is to significantly reduce waste footprints and the environmental impact of the various categories of mine wastes. This can be achieved by integrating geometallurgical characterisation, appropriate database structures, and modelling methods throughout the life-of-mine. However, these methods must be simple, complementary to existing workflows, and, where possible, effective at identifying repurposing opportunities. From deposit-scale to microscale, technologies exist to help acquire mineralogical and textural data, in both 2D and 3D, to enhance the environmental management process. Understanding how and when to use these technologies is the key to unlocking their transformative power and gain maximum insight from multidimensional data sets—using appropriate data science tools (statistics, machine learning, artificial intelligence) that may still need to be developed. A dynamic approach with structured data, such as semantic networks, databases, time series, and dynamic block models, will bring geometallurgical characterisation to its full efficiency, especially for heterogeneous, man-made deposits like tailings and waste rock.
As the raw materials industry transitions towards a more ESG-cognisant outlook, the growing importance of the valorisation of residues, designed from the outset of a mining project, is not to be ignored and speaks to circular economy principles. Valuable data to inform this strategic decision-making process exist already, to some degree, in geometallurgical and chemical assay databases. Yet, the geoenvironmental sector has been slow to embrace the insight that can be gleaned from new characterisation technologies. As mining progresses, a cultural shift towards fingerprinting the characteristics of waste streams, measured using sensor technologies integrated into vehicles, belts, or pipelines, must be enacted to collate data relevant to temporal transitions, as new commodities become important to fuel the technologies of the future. As we revisit old mine wastes, geophysical tools must be better integrated into the characterisation workflow to improve our understanding of the mineralogical and physical properties, and to help build better geospatial models to guide future remining activities. For mines that produce significant quantities of waste (e.g., open cut metalliferous mines), a multi-commodity factory instead of a singleelement extractive operation (with a few by-products at most) is potentially the only solution to really reduce mine wastes. That all residues, economic or not at a given point in time, are so well understood that they can turn economic at a future date is certainly the vision for which the raw materials industry should aim. This may well put it at the centre of a global sustainable circular economy.
ACKNOWLEDGMENTS
The authors would like to thank the two reviewers and editors for their productive comments to improve the clarity of this article.
REFERENCES
Barton IF and 5 coauthors (2021) Extending geometallurgy to the mine scale with hyperspectral imaging: a pilot study using drone and ground-based scanning. Mining, Metallurgy & Exploration 38: 799-818, doi: 10.1007/ s42461-021-00404-z
Blannin R, Frenzel M, Tolosana-Delgado R, Gutzmer J (2022) Towards a sampling protocol for the resource assessment of critical raw materials in tailings storage facilities. Journal of Geochemical Exploration 236: 106974, doi: 10.1016/j. gexplo.2022.106974
Buettner P and 5 coauthors (2018) Recovery potential of flotation tailings assessed by spatial modelling of automated mineralogy data. Minerals Engineering 116: 143-151, doi: 10.1016/j.mineng.2017.09.008
Butcher AR, Dehaine Q, Michaux SP (2023) Characterisation of ore properties for geometallurgy. Elements 19: 352-358
Chetty D, Nwaila GT, Xakalashe B (2023) Fire and water: geometallurgy and extractive metallurgy. Elements 19: 365-370
Dong C, Taylor MP (2017) Applying geochemical signatures of atmospheric dust to distinguish current mine emission from legacy sources. Atmospheric Environment 161: 82-89
Frenzel M, Baumgartner R, Tolosana-Delgado R, Gutzmer J (2023) Geometallurgy: present and future. Elements 19: 345-351
Golev A and 11 coauthors (2022) Ore-sand: a potential new solution to the mine tailings and global sand sustainability crises – final report. The University of Queensland & University of Geneva, 105 pp
Hudson-Edwards K, Lottermoser BG, Jamieson H (2011) Mine wastes: past, present, future. Elements 7: 375-380, doi: 10.2113/gselements.7.6.375
Ighalo JO and 8 coauthors (2022) A review of treatment technologies for the mitigation of the toxic environmental effects of acid mine drainage (AMD). Process Safety and Environmental Protection 157: 37-58, doi: 10.1016/j.psep.2021.11.008
Kefini KK, Msagati TAM, Mamba BB (2017) Acid mine drainage: prevention, treat-ment options, and resource recovery: a review. Journal of Cleaner Production 151: 475-493, doi: 10.1016/j.jclepro.2017.03.082
Kinnunen P, Karhu M, Rantala EY, Kivikytö-Reponen P, Mäkinen J (2022) A review of circular economy strategies for mine tailings. Cleaner Engineering and Technology 8: 100499, doi: 10.1016/j. clet.2022.100499
Laukamp C, Legras M, Lau I (2021) Hyperspectral proximal sensing instru-ments and their applications for explo-ration through cover. In: Crocombe R, Leary P, Kammrath B (eds) Portable Spectroscopy and Spectrometry. Volume 2. Wiley, Hoboken, pp 401-422, doi: 10.1002/9781119636489.ch40
Lottermoser BG (2010) Mine Wastes: Characterization, Treatment and Environmental Impacts. Springer, 400 pp
Maus V and 8 coauthors (2022) An update on global mining land use. Scientific Data 9: 433, doi: 10.1038/s41597-022-01547-4
Mollehuara-Canales R, Kozlovskaya E, Lunkka JP, Moisio K, Pedretti D (2021) Non-invasive geophysical imaging and facies analysis in mining tailings. Journal of Applied Geophysics: 192: 104402, doi: 10.1016/j.jappgeo.2021.104402
Moncur MC, Ptacek CJ, Lindsay MBJ, Blowes DW, Jambor J (2015) Long term mineralog-ical and geochemical evolution of sulfide mine tailings under a shallow water cover. Applied Geochemistry 57: 178-193, doi: 10.1016/j.apgeochem.2015.01.012
New South Wales Environment Protection Authority (2016) Licence Variation of Environment Protection Licence No. 2688. New South Wales Environmental Protection Authority
Parbhakar- Fox A, Lottermoser, BG (2015) A critical review of acid rock drainage prediction methods and practices. Minerals Engineering 82: 107-124, 10.1016/j.mineng.2015.03.015
Parbhakar-Fox A (2019) Reinventing the wheel: the environmental geometallurgy matrix and its supporting tools. Procemin Geomet 2019, Santiago, Chile
Penrose B and 6 coauthors (2022) Heavy metal wombats? Metal exposure pathways to bare-nosed wombats (Vombatus ursinus) living on remediated tin mine tailings. Science of the Total Environment 835: 155526, doi: 10.1016/j. scitotenv.2022.155526
Pereira L, Schach E, Tolosana-Delgado R, Frenzel M (2023) All about particles: modelling particle behaviour in mineral processing. Elements 19: 359-364
Robben C, Wotruba H (2019) Sensor-based ore sorting technology in mining—past, present and future. Minerals 9: 523, doi: 10.3390/min9090523
Robertson PK, de Melo L, William DJ, Wilson GW (2019) Report of the Expert Panel on the Technical Causes of the Failure of the Feijao Dam I. Report, December 12, 2019, Expert Panel on the Feijao Dam I: Brazil, 81 pp
Rogers AJ (2018) Exposures estimates of the Wittenoom mining workforce and town residents – implications associated with risk estimation for persons exposed to asbestiform riebeckite. Toxicology and Applied Pharmacology 361: 168-170, doi: 10.1016/j.taap.2018.06.032
Tayebi-Khorami M, Edraki M, Corder G, Golev A (2019) Re-thinking mining waste through an integrative approach led by circular economy aspirations. Minerals 9: 286, doi: 10.3390/min9050286
Vale (2020) Vale opens factory that trans-forms mining waste into products for civil construction. Vale News, 17 November 2020
Valenta RK and 12 coauthors (2023) Decarbonisation to drive dramatic increase in mining waste – options for reduction. Resources, Conservation and Recycling 190: 106859, doi: 10.1016/j. resconrec.2022.106859
Whitworth A and 5 coauthors (2022) Review on advances in mineral processing technologies suitable for critical metal recovery from mining and processing wastes. Journal of Cleaner Engineering and Technology 7: 100451, doi: 10.1016/j. clet.2022.100451
Wilson R, Toro N, Naranjo O, Emery X, Navarra A (2021) Integration of geosta-tistical modelling into discrete event simulation for development of tailings dam retreatment applications. Minerals Engineering 164: 106814, doi: 10.1016/j. mineng.2021.106814