December 2023 Issue Table of Contents
Geometallurgy is an interdisciplinary research field concerned with the planning, monitoring, and optimisation of mineral resource extraction and beneficiation. Geometallurgy relies on a quantitative understanding of primary resource characteristics such as mineralogical composition and texture, the spatial distribution and variability of these characteristics, and how they interact with mining and beneficiation processes. Thus, geometallurgy requires accurate analytical data for resource characterisation and detailed models of orebody geology, mining and processing technologies, mineral economics, and the often-complex interactions between them. Here, we introduce the fundamental concepts relevant to the field, with particular emphasis on the current state-of-the-art and some notes on potential future developments.
1811-5209/23/0019-0345$2.50 DOI: 10.2138/gselements.19.6.345
Keywords: Raw materials; sustainability; value chains; resource efficiency
INTRODUCTION
Mining and the production of minerals and metals have been crucial for the development of human civilisation. They are set to retain this role for the foreseeable future. This is mostly due to continuing global population growth and economic development, as well as the increasing shift towards renewable energy production and electromobility, technologies that are much more raw-material intensive than fossil fuels or nuclear energy (Vidal et al. 2013). These developments are expected to drive up the global demand for minerals and metals over the coming decades. Unfortunately, recycling alone cannot cover this added demand. Mining will have to fill the gap (International Energy Agency 2022).
Meeting this rapidly increasing demand poses a significant challenge for the global minerals industry. Not only has the quality of various types of mineral deposits available for extraction decreased over the past 100 years (e.g., Mudd et al. 2013, 2017), but it has also become increasingly difficult to find new commercially viable deposits. This has important economic and environmental implications, because lowerquality ores, which typically contain less metal in more complex mineral associations, require more energy for metal extraction and result in the production of larger volumes of waste. Counteracting the detrimental effects of these developments requires substantial increases in the energy and resource efficiency of mining and processing operations.
Geometallurgy is an interdisciplinary research field that addresses this important problem. Its major goal is to maximise the efficiency and environmental sustainability of mining and processing operations through a detailed understanding of ore characteristics, ore variability, and their influence on operational performance. This article introduces the main concepts relevant to the field, including a glossary of the key terms used in this issue (Box 1), and briefly describes the status of academic research and industrial application. The subsequent articles in this issue then explore the most important aspects in more detail.
HISTORICAL PERSPECTIVE
The concept to use the geological and mineralogical understanding of mineral resources for the planning of mining and mineral processing operations is not new. Its origins can be traced at least as far back as the writings of Georgius Agricola (Agricola 1556), but it is probably much older.
Simple quantitative approaches to this problem started to appear in the mineral processing literature of the late 19th and early 20th centuries, clearly recognising the importance of mineralogy and texture for the process responses of ores (e.g., Gaudin 1939). However, the term geometallurgy as a crossover between geology and metallurgy was only coined in 1968 by McQuiston and Bechaud (1968), recognising the necessity for close collaboration between geoscientists and engineers in mining operations. Over the past 20–30 years, such collaboration has greatly benefited from rapid improvements in quantitative analytical techniques, which have also enabled the more widespread implementation of modern geometallurgical workflows. Relevant analytical techniques include scanning electron microscope (SEM)-based image analysis (also called automated mineralogy; Fandrich et al. 2007), multi-element geochemical analyses, quantitative X-ray powder diffraction, laser ablation-inductively coupled plasma mass spectrometry (LA-ICP-MS), and various forms of drill-core scanning as described in more detail by Butcher et al. (2023 this issue).
WHAT IS AN ORE AND HOW DOES IT BEHAVE?
Perhaps the most central concept in geometallurgy (and mining in general) is that of an ore, a geological material, usually a rock, from which a mineral or metal can be extracted at a profit (Robb 2020). Ores generally consist of a variable mixture of ore minerals, i.e., those of commercial interest, and gangue minerals, i.e., the waste. To produce a marketable product, the ore and gangue minerals must be separated (Wills and Finch 2015), usually by physical, physicochemical, or chemical means. If a metal or other pure substance is the final product, additional chemical processing steps may be necessary (Dunne 2019). In a few rare cases, only chemical processes are needed, e.g., for the in-situ leaching of uranium ores (Haque and Norgate 2014), or if the ores are not rocks at all, such as in lithium-rich brine deposits (Kesler et al. 2012).
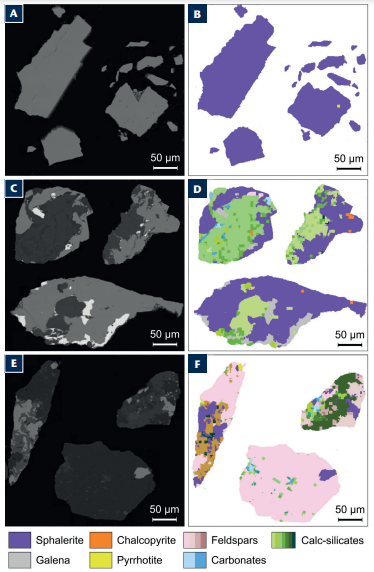
Figure 1 schematically illustrates the most common process chain from ore to metal. A volume of ore (in mining terms, a block) is first drilled and blasted to allow removal from the ground. The ore is then transported (= hauled) to a mineral processing plant, where it passes through the primary crusher, is stockpiled, and subsequently blended with ore from other blocks. Next, the ore blend is crushed further and milled to reduce it to small fragments, called particles. This fragmentation process, called comminution, has the goal to free up as many of the grains of the ore mineral(s) as possible to produce separate particles (Wills and Finch 2015). The degree to which this is achieved is described as mineral liberation. Different mineral separation processes are then applied to the particles, acting on the specific physical or physico-chemical properties of the minerals within them to separate ore mineral(s) from gangue minerals. The result is one or more mineral concentrates containing the desired ore mineral(s), as well as one or more streams of fine-grained waste material or tailings. Tailings, as well as coarser, uncrushed, rock material removed to access the ore (= waste rock), are deposited in piles and dams near the mine site. The ore mineral concentrates are dewatered and transported to pyrometallurgy or hydrometallurgy plants where they undergo the necessary chemical transformations to produce pure metals or other substances suitable for use by downstream industries, a process known as extractive metallurgy. This transformation results in the formation of further residues, e.g., slags, dusts, and slimes, typically deposited near the smelter or hydrometallurgy plant.
An alternative processing route is the direct leaching of the crushed and milled ore using reagents and/or bacteria in an aqueous medium, followed by chemical extraction of the metals from the resulting solution. This is typically done at the mine site, with the leached ore remaining as the main residue.
The success of the various extraction processes is generally measured in terms of how much material is being mined and processed within a given unit of time (= throughput), what proportion of the ore minerals or metals contained in the ore are extracted into products (= recovery), and how much energy, chemicals, tools, and labour are expended to do so (= operational expenditure (OPEX)) (cf. Dominy et al. 2018; Olson-Hoal and Frenzel 2022). Other aspects include the overall sales value of the products, environmental impacts of the mine, the amount and nature of the generated waste materials, and the requirements for their storage, disposal, and/or remediation after mine-closure, as well as the original investment costs (= capital expenditure (CAPEX)). The inherent geological characteristics of an ore enact a strong influence on all these aspects, as follows:
- Ore hardness, or its resistance to fragmentation, is a direct function of modal mineralogy (e.g., the content of hard minerals like quartz or topaz) and the scale of mineral intergrowths, i.e., ore texture. Thus, these properties exert a major control on throughput and energy consumption.
- Ore texture, in particular grain size, controls the final particle size that must be achieved by comminution. This, in turn, controls the ultimate recoverability of the minerals and metals. More finely intergrown ores must be milled to finer particle sizes to achieve mineral liberation, causing higher energy consumption and OPEX, and produce chemically more reactive tailings. Figure 2 shows some ore particles with varying degrees of liberation resulting from comminution.
- The nature of the ore and gangue minerals dictates which types of separation processes are appropriate for a given ore. For instance, magnetic separation is only sensible when ferro- or strongly paramagnetic minerals are present.
- The spatial associations of the different minerals, resulting in their co-occurrence or separation in different ore particles, control recovery options and product quality. For instance, if two minerals co-occur as extremely fine intergrowths, then they may have to be recovered into a single product and separated during metallurgical treatment. Alternatively, substantial losses of valuable material may occur if these intergrowths are discarded.
- Ore grade, or the concentration of the valuable components in the ore, strongly controls the total sales value of the final product(s), with total revenues mostly related to grade × throughput × recovery × price.
- In waste rocks and tailings, the balance between minerals prone to acid generation when exposed to air (e.g., pyrite) and those with acid-neutralising properties (e.g., calcite) directly controls the potential for acid mine drainage generation (Parbhakar-Fox and Baumgartner 2023 this issue). This, in turn, controls waste storage and disposal options, as well as remediation costs.
Box 1
GLOSSARY OF GEOMETALLURGY TERMS
Definitions are provided here strictly as used in
this issue. Other common usages are highlighted
where relevant.
Association (of minerals) – The degree of intergrowth of one mineral with another, generally measured as the proportion of the total grain surface area of the first mineral in contact with grains of the second.
Beneficiation – General term for the upgrading of a raw material to a more valuable product; typically including both mineral processing and extractive metallurgy.
Block (of ore) – A volume of ore in a deposit; often corresponds to the smallest volume that can be mined separately.
Block model – A geospatial model of an ore deposit in which the characteristics of each ore block are inferred from data collected on drill-core and mine faces.
CAPEX – Capital expenditure; the investment costs required to find, build, and open a mine.
Classification – The process of separating a crushed or ground material into different size fractions.
Comminution – The process of size reduction: blasting, crushing, and grinding.
Concentrate – An enriched product consisting mostly of ore minerals, produced by a mineral processing plant (comminution and mineral separation).
CRM (= critical raw material) – A raw material deemed economically essential, with simultaneously high supply risk.
Crushing – The process of size reduction at particle sizes above ~3 mm; often done using cone or jaw crushers.
Deportment (of an element) – The quantitative allocation of an element to different minerals in an ore sample, e.g., the percentage of the total gold content present in pyrite and as free gold in a gold ore; an important parameter for process design.
Extractive metallurgy – The operation of extracting metals from their ores through a series of chemical transformations; subdivided into hydrometallurgy and pyrometallurgy according to the chief medium of extraction.
Feed (ore) – The material delivered to a mineral processing plant.
Gangue (minerals) – The non-valuable minerals in an ore.
Geostatistics – The branch of statistics concerned with the description and modelling of the spatial (or spatiotemporal) distribution of variables.
Grade (of a metal) – The concentration of a metal in an ore. Grain – Generally, a crystal of a single mineral in a rock or particle, separated from other grains by grain boundaries.
Grinding – Also called milling; the process of size reduction at particle sizes below ~3 mm, for example in ball mills or semi-autogenous grinding (SAG) mills.
Hardness – Generally, a measure of the energy required to crush or grind a given mass of material to a specific size.
Hydrometallurgy – An extractive metallurgical process where chemical transformations in aqueous solutions are used to extract the metal(s) from an ore or mineral concentrate, e.g., heap leaching.
Liberation (of a mineral) – The degree to which grains of a mineral in a milled ore occur in separate particles, generally expressed as the mass fraction (volume liberation) or surface area fraction (surface liberation) of a particle, which consist of that mineral.
Metallurgy – The science of extracting metals from their ores, generally subdivided into mineral processing and extractive metallurgy, respectively, referring to physical and chemical separation processes. In more general usage, the term metallurgy can also be used to refer to the branch of materials science dealing with the further manufacture of metal products and alloys.
Mineral processing – Sometimes also minerals processing; the operation of crushing, grinding, and separating an ore into one or several concentrates of the ore minerals and tailings.
Mineral separation – The operation of separating minerals from milled ore through physical (e.g., density separation) or physico-chemical (e.g., froth flotation) processes.
Model – An informative representation of an object or system; in geometallurgy, generally a mathematical description of a geological body or industrial process.
Net present value (NPV) – The current value of a mining project, calculated by subtracting CAPEX from the sum of all expected future cashflows (revenue minus OPEX), discounted back to the present.
OPEX – Operating expenditure; the annual cost of operating a mine.
Optimisation – The selection of the best scenario for something (mine plan, processing plant design, etc.) with regard to some quantitative criterion; usually done by maximising or minimising a specific mathematical function.
Ore – A geological material, generally a rock, from which a metal or mineral can be extracted at a profit.
Particle (of ore) – A generally small (<3 mm) rock fragment consisting of one or several mineral grains.
Penalty element – A deleterious, often toxic, element present in a mineral concentrate, which negatively affects downstream extractive metallurgy processes, and for which a penalty must therefore be paid by a mine, e.g., As in Cu ores.
Primary (ore) characteristics – The inherent properties of a rock or ore, including its geochemical or mineralogical composition, texture, density, porosity, etc.
Pyrometallurgy – An extractive metallurgical process where high temperatures are used to induce chemical transformations in a mineral concentrate and extract the metal(s), e.g., in a blast furnace.
Recovery (of minerals/metals) – The relative amount of a mineral or metal recovered in a concentrate stream, expressed as a fraction of the mass of the minerals/metals contained in the feed material.
Reserve (of a commodity) – The economically extractable amount of a commodity within a resource, accounting for the dilution and losses which occur during mining and processing.
Resource (of a commodity) – The total amount of a commodity which has been shown to be present within an ore deposit by drilling, at a maximum degree of uncertainty. Different categories (measured, inferred, indicated) exist according to the estimated level of uncertainty.
Secondary (ore) characteristics – The behaviour of a rock or ore in a specific process, e.g., its grinding hardness, leachability, flotation behaviour, etc.
Texture (of an ore) – The overall 3D structure of an ore resulting from the combination of sizes, shapes, orientations, and intergrowth relationships of individual mineral grains, voids, and fractures.
Tailings – The fine-grained waste material remaining after crushing and grinding of an ore, and separation of the valuable minerals.
Throughput – The amount of feed processed by a mineral processing or extractive metallurgy plant in a given unit of time, typically stated in tonnes/day.
Waste rock – The non-ore rock material extracted to access ore.
VARIABILITY AND UNCERTAINTY
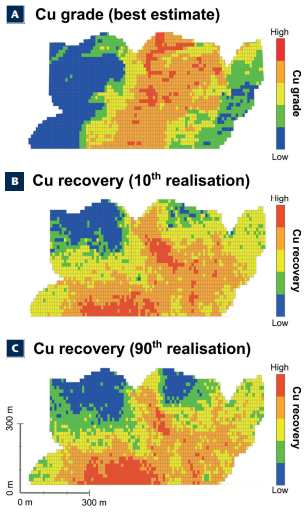
The previous section provided some insights into how different ore characteristics influence the way in which ores are processed. However, it did not discuss the influence of the inherent spatial variability of these characteristics within a deposit. Ore deposits are geological bodies of unusual composition and are often the product of a complex sequence of geological events with spatially varying characteristics. Many ore-forming systems, be they magmatic, hydrothermal, or sedimentary, comprise strong thermal and/or chemical gradients, resulting in corresponding gradients in the mineralogical composition and texture of the ores. The resultant deposits may later be overprinted and partially remobilised by metamorphic events, again resulting in spatially varying changes to ore textures and mineralogy. Exhumation and weathering may cause further changes. Figure 3A shows an example cross section through a copper deposit, illustrating the spatial variability in Cu grade.
Because we cannot exhaustively characterise an ore deposit before mining, but only have access to about 1/10,000th to 1/1,000,000th of the total volume through drill-core, this inherent geological variability causes considerable uncertainties with respect to the true in-situ characteristics of the ores and their spatial distribution, which will be encountered during mining and beneficiation (cf. Dominy et al. 2018). Figure 3B and 3C illustrate this for the example in Figure 3A, showing several potential distributions of Cu recovery compatible with the observed data. The poor correlation between Cu grade and Cu recovery should be noted. This is due to Cu recovery being chiefly controlled by ore properties unrelated to Cu grade, such as texture and gangue mineralogy.
This uncertainty causes problems during the mining and processing of the ore. Current mineral processing plants are optimised to operate under relatively static conditions (hence, the stockpiling and blending of different ore blocks in the plant feed; Fig. 1). Therefore, unpredictable variations in feed characteristics will cause suboptimal processing performance. Unfortunately, the true extent of ore variability and its effects on downstream process outcomes are not well characterised in many operations. This is the principal reason why more than half of all new mining operations fail to reach projected performance targets (Carlson 2019). Thus, a major aspect of all geometallurgical studies is the quantification of uncertainties, and if possible, their reduction. Ortiz et al. (2023 this issue) provide a more detailed account of ore variability, uncertainties, and how they can be dealt with.
CURRENT GEOMETALLURGY WORKFLOWS
What exactly does geometallurgy do to achieve its goals? Geometallurgical studies often consist of a general series of steps. These are schematically illustrated in Figure 4. This general sequence is independent of the specific goals of a study. However, adjustments are generally made in the design and execution of the individual steps to fit specific cases.
First, a sampling scheme is designed to collect relevant, representative samples for the problem at hand. If the problem is an initial geometallurgical assessment of an ore deposit during the exploration stage, this will cover ore samples representing the range of geological variability present within the deposit as recognised by the site geologists. If, on the other hand, the goal is to solve a problem within an existing operation, sampling may focus on the mineral processing plant. Sampling schemes generally consider as much of the available information as possible to yield an effective selection of typically tens to hundreds of samples.
Second, the samples are characterised for relevant ore properties. This generally includes primary ore characteristics such as mineralogy, texture, and geochemical composition (Butcher et al. 2023 this issue), as well as process responses, commonly referred to as secondary characteristics (Pereira et al. 2023 this issue). These responses may be observed directly by tracking specific volumes of ore through a running processing plant, or they may be approximated by standardised laboratory tests.
Third, the characterisation data are integrated to yield quantitative predictive models that relate the secondary ore characteristics to primary ones. These models must generally be extrapolatable to the entire ore deposit. Because the samples with detailed mineralogical, textural, and metallurgical test data generally cover only a small part of the available drill-core material, this is currently achieved by directly correlating specific secondary ore characteristics with multi-element geochemistry and geological drillcore logs. Such data are usually available with good spatial coverage. Image data from various drill-core scanning methods (optical, hyperspectral, XRF, etc.) are becoming another important input for this purpose.
Fourth, the extrapolated predictive outputs from the models covering the entire deposit are used for optimisation. The optimisation process may include the mining methods, mine schedule, processing plant design, and waste disposal methods, depending on the scope of the geometallurgical study. A commonly optimised function in current operations is the net present value (NPV) of the ore deposit. This is calculated by subtracting CAPEX from the sum of all expected future cashflows (revenue minus OPEX), discounted back to the present day via an average discount rate, or
where i is the year, d is the discount rate, and LOM is the total life-of-mine, expressed in years. Other measures that can be optimised include metal or mineral recoveries (= resource efficiency), greenhouse gas emissions (e.g., Pell et al. 2019), and other environmental impacts.
Finally, true operational outcomes are used to validate the predictions from the geometallurgical modelling and adjust relevant models where these fail to provide accurate predictions. This process is known as reconciliation. As the circular shape of Figure 4 suggests, geometallurgy programs are not linear processes, but rather proceed as a series of iterations throughout the lifetime of a mine.
EXAMPLE
To conclude the description of the current state of geometallurgy, the following case from the literature provides an example of the application and benefits of state-of-the-art geometallurgical workflows. The results of mineralogical and geochemical analyses, combined with variability testing, estimations, and simulations are integrated into the ore deposit model to provide reliable process performance predictors and reduce uncertainty and associated technical risks. Iterative reconciliations of this geometallurgical model with actual performance have provided higher confidence and, thus, better operational results.
Case Study: Olympic Dam, Australia
Olympic Dam is a large, breccia-hosted, Fe-oxide Cu–U– Au–Ag deposit in Australia. Due to the complexity of the ore with over 100 minerals present (Ehrig 2021), the beneficiation strategy is complex and involves multiple processing steps to make the overall recovery economic and the resulting products saleable. Each mineral has its own unique response to each part of the mineral processing plant (Ehrig 2021). Therefore, the type of minerals present in an ore block is one of the most important drivers of overall process performance. For these reasons, a geometallurgical approach was adopted to plan and monitor the operation. It consists of a routine mineralogical and geochemical characterisation of ore and waste. Over 30 elements are analysed, and the abundances of the more than 100 minerals are quantified via SEM-based image analysis from holes drilled ahead of production. The most impactful elements and minerals are directly included in the deposit model via interpolation, only possible due to the high data density. These are subsequently used in mathematical models to estimate each metallurgical parameter for which direct information is not available, enabling an assessment of expected metallurgical behaviour for each ore block contained in the model (Ehrig 2013; Liebezeit et al. 2016). The deposit model containing all this block-specific data then serves as the major input for the optimisation of the mine plan.
Over the years, the geometallurgical model at Olympic Dam has permitted a reduction of the technical risks of current and future operations by identifying areas of positive- and negative-impact materials, increasing the confidence of predictions, and providing the data necessary to comply with regulatory mining codes (Ehrig 2013; Liebezeit et al. 2016).
OUTLOOK
Despite their obviously positive impact on operations, current geometallurgy workflows are still not widely applied by the minerals industry. Furthermore, current workflows are mostly limited to the mine site, i.e., from excavation to mineral separation, and do not consider the impact of mineral concentrate composition on the performance of extractive metallurgy (Chetty et al. 2023 this issue). Similarly, predictions of environmental performance are often omitted (Parbhakar-Fox and Baumgartner 2023 this issue). Finally, there is still room for substantial future improvements in predictive power and thus mining outcomes. For instance, the prevalent use of multi-element geochemical data to extend predictions of process outcomes across a deposit has limited power where ore textures are a chief control on the variation of these outcomes (Pereira et al. this issue). The optical or SEM-based methods currently used to quantify ore textures in 2D introduce stereological bias into assessments of particle sizes and mineral liberation, causing losses in predictive power because ore particles are 3D objects (Butcher et al. 2023 this issue). Last but not least, mineral processing plants still operate under relatively static process conditions resulting in avoidable inefficiencies due to feed variability (Ortiz et al. 2023 this issue). Current developments in analytical technology, stochastic geometry, and computational power are rapidly opening new avenues of research to address these efficiency potentials. The most important of these are discussed in more detail in the subsequent articles of this issue.
FURTHER READING
Readers wishing to delve more deeply into the general subjects covered in this issue may find it useful to acquire the following introductory texts on different areas relevant to geometallurgy: Robb (2020) gives a general introduction to ore deposits and their geology; Wills and Finch (2015) and Dunne (2019), respectively, provide up-todate introductions to mineral processing and extractive metallurgy; Rossi and Deutsch (2014) give an overview of resource estimation; and Lottermoser (2007) provides an introduction to mine wastes and associated issues. Finally, Dominy et al. (2018), van den Boogaart and TolosanaDelgado (2018), and Olson-Hoal and Frenzel (2022) provide more detailed perspectives on geometallurgy and include more comprehensive reference lists than possible in the present short review.
ACKNOWLEDGMENTS
We would like to thank Kathryn Goodenough and Kurt Aasly for their reviews of this article, which helped us to improve it significantly. Helmholtz-Zentrum DresdenRossendorf is thanked for funding open access to this article.
REFERENCES
Agricola G (1556) De re metallica. Translated by Hoover HC and Hoover LH. Dover Publications, Inc., 638 pp
Butcher AR, Dehaine Q, Menzies AH, Michaux SP (2023) Characterisation of ore properties for geometallurgy. Elements 19: 352-358
Carlson R (2019) Understanding geologic uncertainty in mining studies. SEG Discovery 117: 21-29, doi: 10.5382/ Geo-and-Mining-03
Chetty D, Nwaila GT, Xakalashe B (2023) Fire and water: geometallurgy and extractive metallurgy. Elements 19: 365-370
Dominy SC, O’Connor L, Parbhakar-Fox A, Glass HJ, Purevgerel S (2018) Geometallurgy – a route to more resilient mine operations. Minerals 8: 560, doi: 10.3390/min8120560
Dunne RC (2019) SME Mineral Processing and Extractive Metallurgy Handbook, Volume 2. Society for Mining, Metallurgy and Exploration, 2312 pp
Ehrig K (2013) Geometallurgy – what do you really need to know from exploration through to production? In: Proceedings MetPlant 2013, The Australian Institute for Mining and Metallurgy, Melbourne, pp 28-33
Ehrig K (2021) The discovery and mining of the Olympic Dam deposit: impacts on the optimization of exploration and mining/ processing of complex ores. In: SEG
100 Conference Proceedings, Society of Economic Geologists
Fandrich R, Gu Y, Burrows D, Moeller K (2007) Modern SEM-based mineral libera-tion analysis. International Journal of Mineral Processing 84: 310-320, doi: 10.1016/j.minpro.2006.07.018
Gaudin AM (1939) Principles of Mineral Dressing. McGraw-Hill, 554 pp
Haque N, Norgate T (2014) The green-house gas footprint of in-situ leaching of uranium, gold and copper in Australia. Journal of Cleaner Production 84: 382-390, 10.1016/j.jclepro.2013.09.033
International Energy Agency (2022) The Role of Critical Minerals in Clean Energy Transitions. International Energy Agency, 283 pp
Kesler SE and 5 coauthors (2012) Global lithium resources: relative importance of pegmatite, brine and other deposits. Ore Geology Reviews 48: 55-69, doi: 10.1016/j. oregeorev.2012.05.006
Liebezeit V and 5 coauthors (2016) Embedding geometallurgy into mine planning practices – practical examples at Olympic Dam. In: Proceedings, Third AusIMM International Geometallurgy Conference 2016, pp 135-144
Lottermoser BG (2007) Mine Wastes. Characterization, Treatment, and Environmental Impacts. Springer, 304 pp
McQuiston FW, Bechaud LJ (1968) Metallurgical sampling and testing. In: Pfleider EP (ed) Surface Mining. The American Institute of Mining, Metallurgical, and Petroleum Engineers, New York, pp 103-121
Mudd GM, Weng Z, Jowitt SM (2013) A detailed assessment of global Cu resource trends and endowments. Economic Geology 108: 1163-1183, doi: 10.2113/ econgeo.108.5.1163
Mudd GM, Jowitt SM, Werner TT (2017) The world’s lead-zinc mineral resources: scarcity, data, issues and opportunities. Ore Geology Reviews 80: 1160-1190, doi: 10.1016/j.oregeorev.2016.08.010
Olson-Hoal KE, Frenzel M (2022) Ores drive operations – economic geology is the foundation of geometallurgy. SEG Discovery 129: 30-43, doi: 10.5382/ Geo-and-Mining-15
Ortiz J and 5 coauthors (2023) Uncertainty and value: optimising geometallurgical performance along the mining value chain. Elements 19: 377-383
Parbhakar-Fox A, Baumgartner R (2023) Action versus reaction: how geometal-lurgy can improve mine waste manage-ment across the life-of-mine. Elements 19: 371-376
Pell R and 7 coauthors (2019) Environmental optimisation of mine scheduling through life cycle assessment integration. Resources, Conservation & Recycling 142: 267-276, 10.1016/j.resconrec.2018.11.022
Pereira L, Schach E, Tolosana-Delgado R, Frenzel M (2023) All about particles: modelling particle behaviour in mineral beneficiation. Elements 19: 359-364
Robb L (2020) Introduction to Ore-forming Processes (Second Edition). Wiley-Blackwell, 496 pp
Rossi ME, Deutsch CV (2014) Mineral Resource Estimation (First Edition) Springer, 332 pp
van den Boogaart KG, Tolosana-Delgado R (2018) Predictive geometallurgy: an interdisciplinary key challenge for mathematical geosciences. In: Daya Sagar BS, Cheng Q, Agterberg F (eds) Handbook of Mathematical Geosciences. Springer, Berlin, pp 673-686.
Vidal O, Goffé B, Arndt N (2013) Metals for a low-carbon society. Nature Geoscience 6: 894-896, doi: 10.1038/ngeo1993
Wills BA, Finch JA (2015) Wills’ Mineral Processing Technology (Eighth Edition). Elsevier, 498 pp